ICP-3D Project
Description
The automotive industry is focusing innovation mainly on electric propulsion and other types of alternative propulsion such as hydrogen, however, the combustion engine still has a long way to go to introduce improvements that increase its efficiency and reduce its environmental impact, complying with the rigorous limits. imposed by the new regulations.
Within the ICP-3D (Industrial Core Printing) project led by Loramendi, whose final client is the automotive giant BMW, a series of innovative machines have been developed for the automatic, large-scale production and through additive manufacturing of cores. sand used for casting cylinder heads, one of the key parts of engines. The manufacture of these cores through 3D printing allows a better design of the cylinder head to increase the efficiency of the combustion engine, which has a positive impact on its parameters, such as noise level, emissions or fuel consumption. This advance is key, beyond the technological issue, to open doors to new innovations through additive manufacturing.
Argolabe has carried out the mechanical design of these innovative machines under the strict technical and regulatory requirements imposed by a project in a sector as competitive as the automotive industry, and for one of the most demanding manufacturers on the market. This project has a strong R&D component as it is part of a pioneering development in the industry, which represents a high technological challenge.
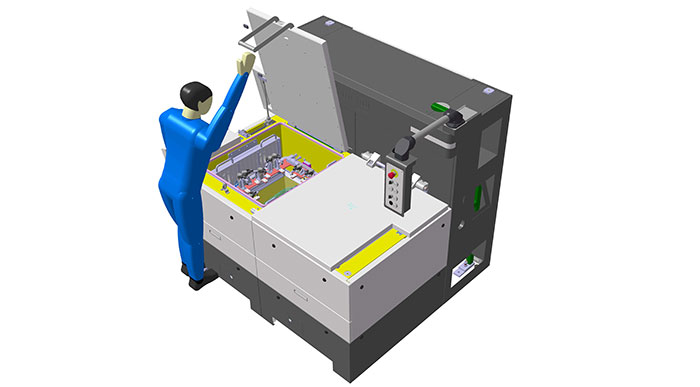
The key to success
Starting from Loramendi’s concept design, Argolabe has developed precise and reliable machines with specific capacities for each stage of the process that make up a line that processes sand cores from their additive manufacturing to their use in the foundry.
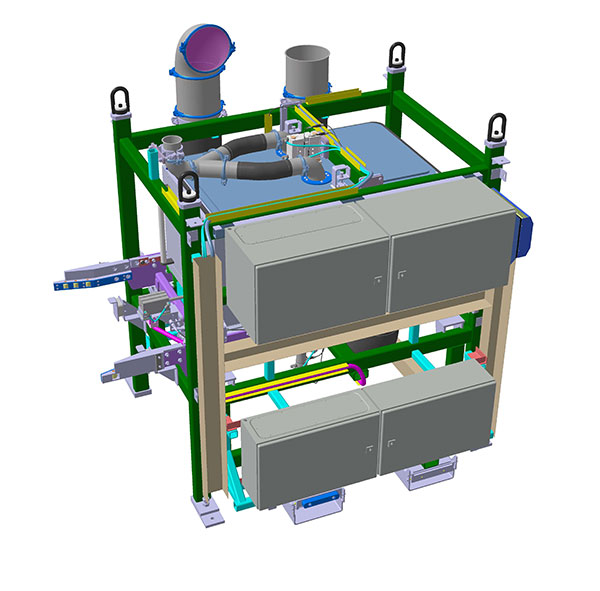
How we achieve this
We have applied the DFX design methodology that seeks a design with a global approach that takes into account reliability, costs, manufacturing, assembly, maintainability and reliable supply chain:
1
Maximum modularity and interchangeability of components between machines.
2
Minimum number of components.
3
Symmetry of components and systems.
4
Error-proof assembly (poka-yokes).
5
Standard element utilization.
6
Standardized fixing systems.
7
Appropriate and reasonable manufacturing tolerances.
8
Robust design of systems and subsystems.
9
Dynamic, kinematic and structural calculations.
10
Analysis of possible failures and their effects.
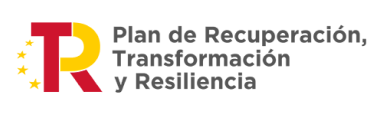
Financiado por la Unión Europea - NextGenerationEU
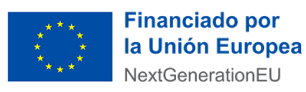